From fastening a jacket pocket to securing solar panels, VELCRO® Brand products are depended on by many brands and users as the Original hook & loop fastener. Many other solutions have emerged, but the VELCRO® Brand has remained as a top choice for many professionals due to the quality of service, culture, engineering and products. Here is how our soon to be implemented Quality 4.0 process will further ensure our products are reliable so that our customers can best serve their consumers.
The Digital Age Has Increased Demand for Data Management
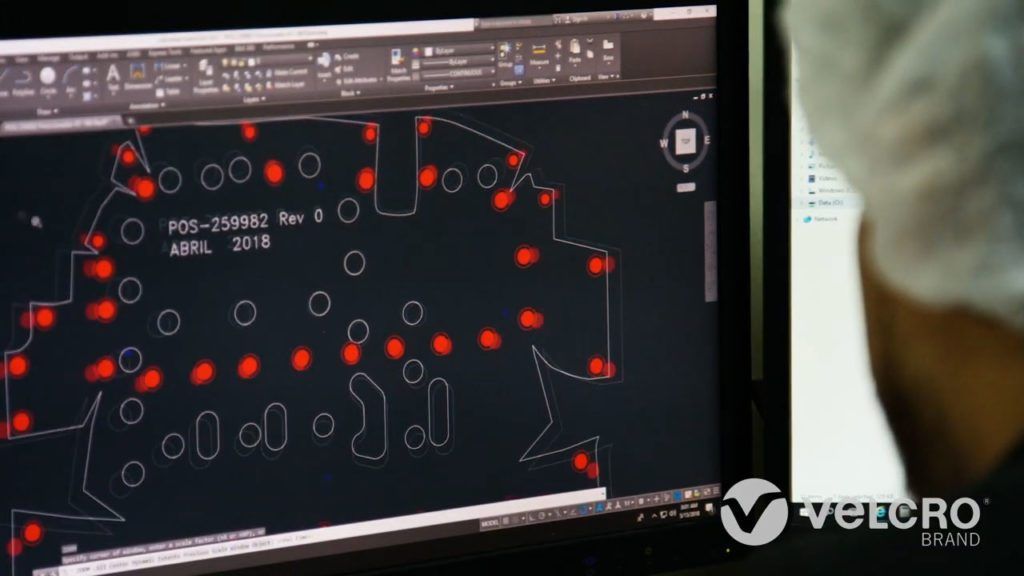
Data, analytics, collaboration, scalability, and connectivity are driving not just innovation but changing how we do business. Technology has helped businesses to store, retrieve and analyze massive amounts of data. Today, we can make fact-based decisions based on reliable information. Harnessing the power of that information can lead to innovation, increased quality, and cost savings.
Quality 4.0 is the Next Generation of Quality Control in Manufacturing
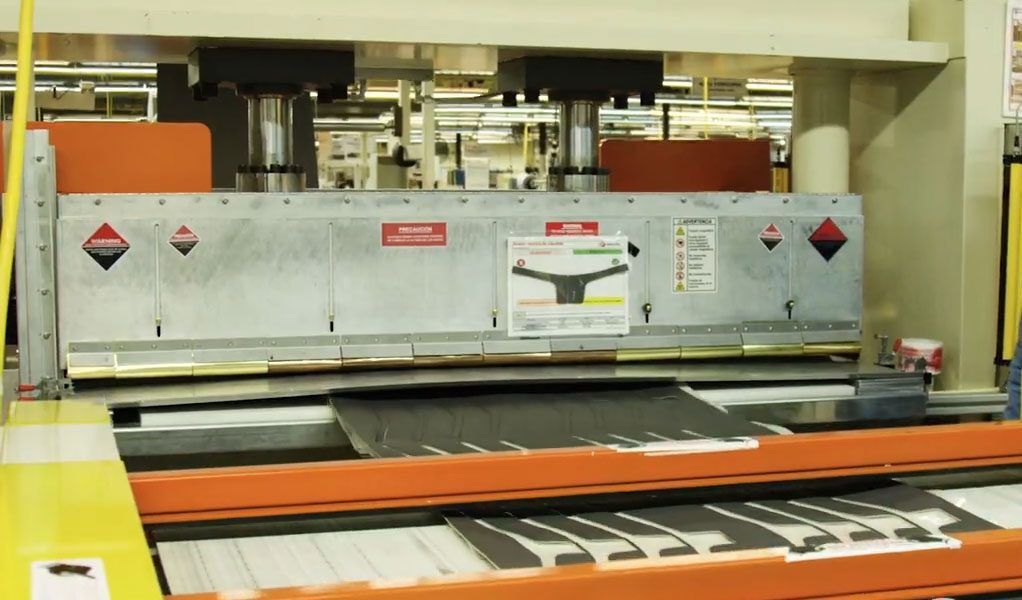
Developing systems and tools to use volumes of data is key to delivering innovative products that meet high-quality standards. Quality 4.0, is the answer to this and at Velcro Companies, we are working on this direction to achieve operational excellence.
Taking a Proactive Approach to Product & Service Quality
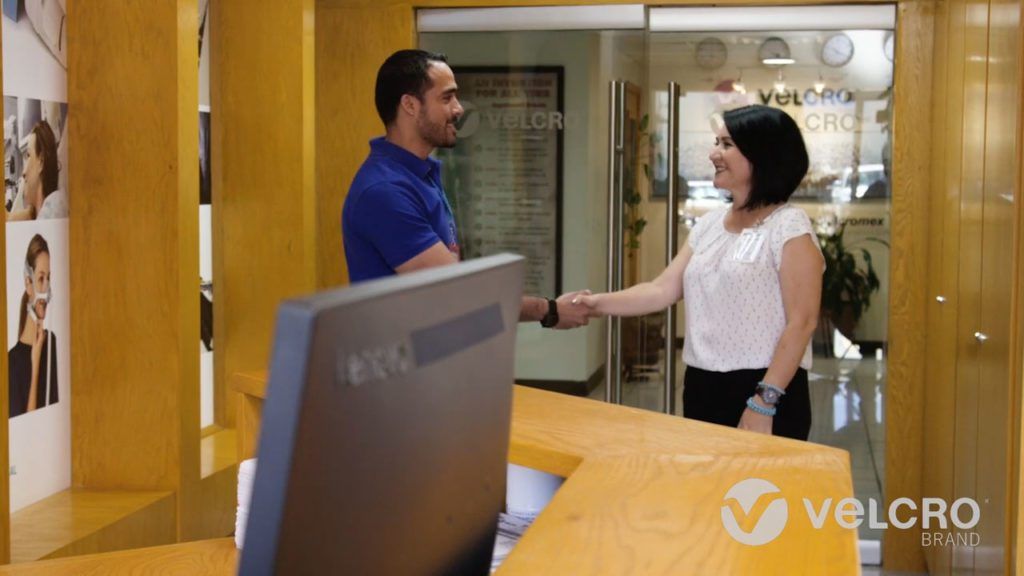
The VELCRO® Brand name has always conveyed superior quality, exceptional performance, and unsurpassed reliability. While some businesses operate in a Quality Control reactive environment trying to stay vigilant and correct problems as they arise, we have a Quality Culture that focuses on defect prevention.
The quality of our culture means that the people in our company are well equipped and committed to our company goals. From the manufacturing floor to the sales and customer service offices, our people are our most valuable assets to delivering the best overall experience for our customers.
We use Process Maps to monitor the performance of our Quality Management System, tracking Effectiveness & Efficiency metrics and reporting progress at regularly scheduled Management Reviews, so we never lose sight of maintaining the quality that our customers expect.
Using predictive analysis upfront in the Design & Development process reduces variation and provides our customers with products that meet their needs consistently. Predicting results based on credible data gives our customers a significant competitive advantage.
Our global manufacturing facilities provide product consistency, regardless of where our customers are located. This provides shorter lead times and reduces complications with import processes. For instance, the automotive industry relies on just in time manufacturing models. Our operations in the Americas, Europe and Asia can easily accommodate for automotive manufacturers to get their components to the assembly line on time.
VELCRO® Brand Quality has become Well Known Across Many Industries, Worldwide
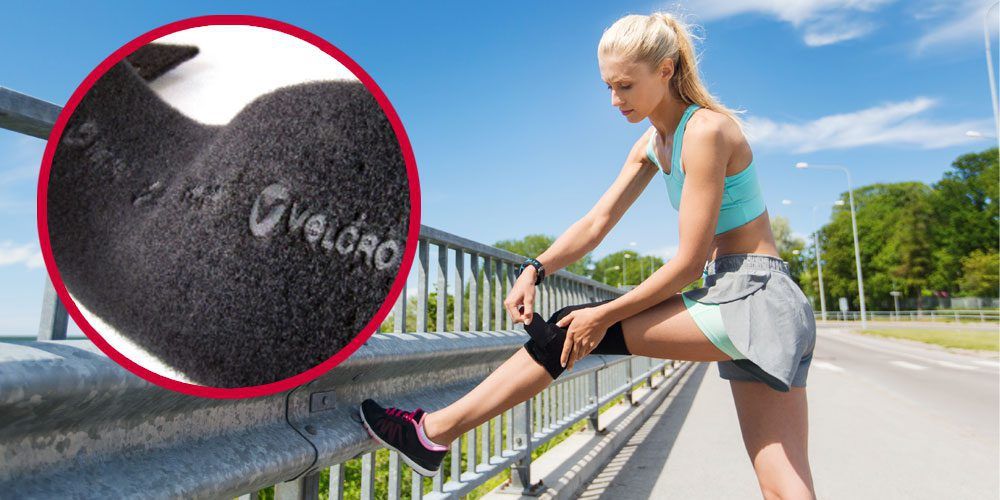
Our extensive experience in medical, automotive, packaging, construction and more allows us to help our customers develop their products in compliance with up-to-date industry standards from the start. Our products can align with standards such as ISO, IAF, REACH, OEKO-TEX® STANDARD 100 and more.
Our focus on the customer means employees have a passion for providing quality products and services. This means we actively listen to customer needs, perspectives and challenges and deliver tailored solutions in a timely manner.
Consumers need to know that the products they use are made of the highest quality components. VELCRO® Brand products can deliver this sense of confidence so that manufacturers can uphold strong relationships with their customers.
Read more about our solutions on the blog: